What is Automotive and Industrial Automation Industry PCBA?
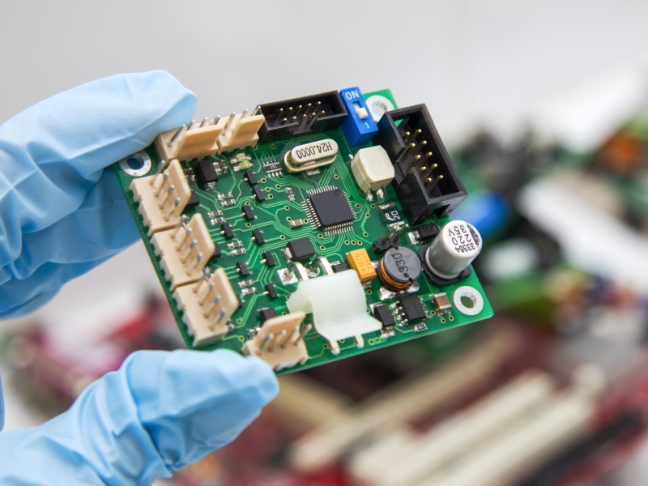
Automotive PCBs are the circuit boards used in automotive electronics from engine controls, anti-lock brake systems, and GPS, to rearview cameras and front lights. Safety is the most important consideration for automotive PCB design and manufacturing.
As more and more electric cars and hybrid electric vehicles drive on roads, the demand for reliable automotive PCBs rises. Automotive PCBs from JH PCBA are specially manufactured and assembled to support every system and application for vehicles.
Automotive PCBs have strict quality requirements, and whole process must be traceable. From the first process to the end, the entire manufacturing process of every automotive PCB board is recorded in a “PPAP level 3 required” report, including material used, manufacturing process flow, operators, machine specifications, quality control details, test reports etc.
The “PPAP level 3 required” report and a COC report are delivered with the automotive PCBs to the buyer. Meanwhile, JH PCBA’s intelligent management system records all information for traceability.
The one-stop automotive PCB manufacturer JH PCBA, an ISO9001 and IATF16949 certified company, provides one-on-one engineering support and custom manufacturing solutions tailored to your needs.
Which parts of the car require PCBs?
Please Check JH PCBA’s Automotive PCBA by products
JH PCBA has many years of experience in the automotive industry since year 2009. JH PCBA’s strategic EMS partner ranks among the top 5 in the world’s largest contract manufacturing supplier of automotive products. It has many years of experience serving Volkswagen, BOSHI, SAIC Motor etc.
Types of Automotive PCBs
Rigid PCBs
-
FR-42, FR-44, FR-46
-
CEM-I, CEM-III
-
Polyimide
-
Rogers
Flexible PCBs
-
Polyimide
-
Kapton
Rigid-Flex PCBs
HDI PCBs
Metal Core PCBs
Ceramic Substrate PCBs
Heavy Copper PCBs
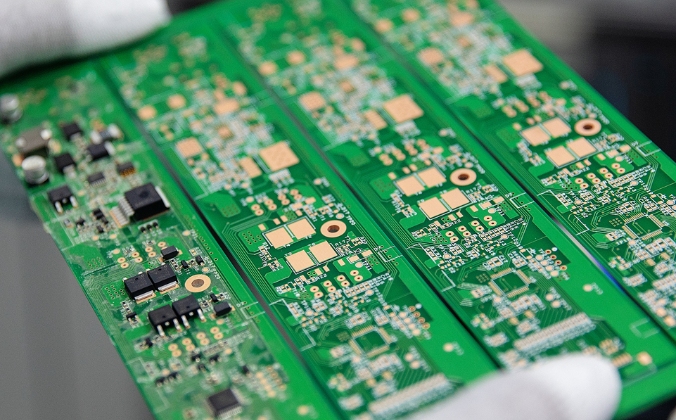
Please check JH PCBA’s Automotive PCBA by PCB types and Material
Key Standards for Automotive PCB Manufacturers
The automotive pcb manufacturers follow these key automotive pcb standards in manufacturing: AEC-Q100/AEC-Q102/AEC-Q200/IPC-6012DA/IATF 16949
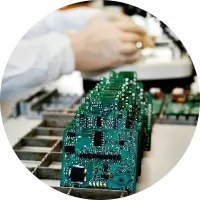
Leading automotive PCB manufacturing and certification
JH PCBA has been providing IPC Class 2/3 PCB manufacturing and assembly since 2009. The automotive industry components that JH PCBA sources are from the most reliable suppliers and traceable. You can check our PCBA certifications, including ISO 9001:2015, IATF 16949:2016, REACH (EC 1907/2006), RoHS (Directive 2002/95/EC), and UL
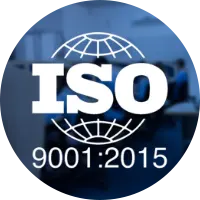
What is Automotive and Industrial Automation Industry PCBA?
1)Harsh Environmental Conditions:
Automotive PCBs must operate reliably under extreme conditions, including wide temperature ranges, humidity, vibrations, and exposure to dust, dirt, and chemicals. Designing for these conditions can be challenging.
①For working temperature range:
The temperature range of the engine compartment is between -40°C and 150°C. Therefore, automotive chips and circuit boards need to meet this wide temperature range, while consumer chips only need to meet 0°C~70°C working environment. More, vehicles are sold worldwide, and different regions often have different environmental characteristics of temperatures and humidity. Therefore, automotive PCBs must be able to adapt to different environments, although some manufacturers make PCBs for specific environments.
In order to reach big working temperature range of automotive PCBs requirement, JH PCBA just use KB, Shengyi
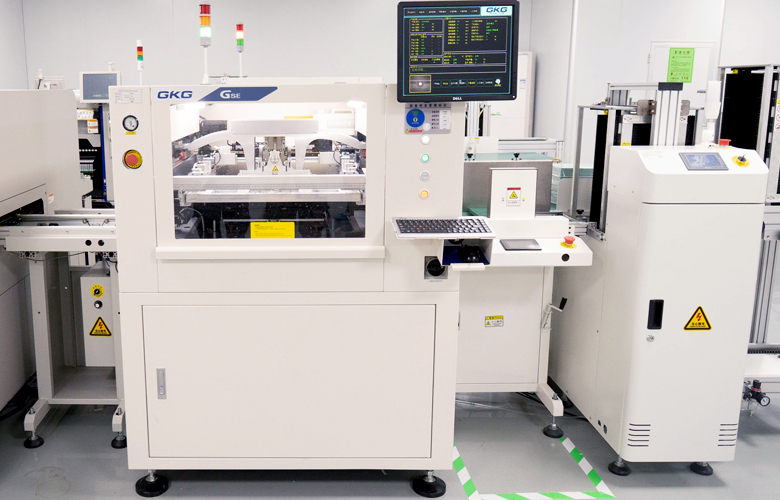
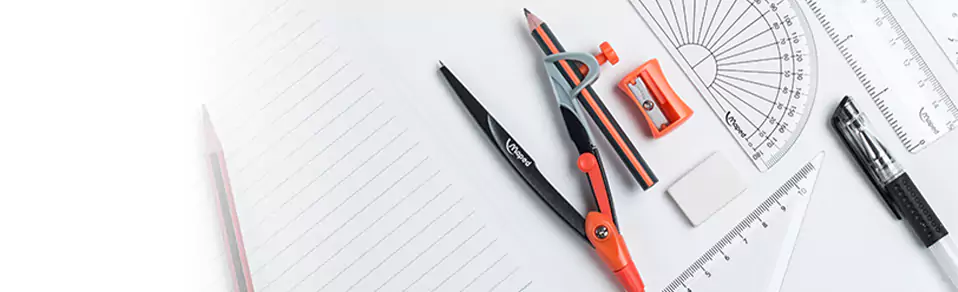
②Vibration and Shock Resistance
Vibration from engine and road noises.
Shock from bumps and unequal road surfaces.
③Resist the threat of dirty and various chemical corrosion
Certain anti-corrosion ability: PCB boards have good resist to the threat of various chemical corrosion such as corrosive acid, organic solvent, salt water, etc.
Resist to the accumulation of dirt during years of operation is critical.
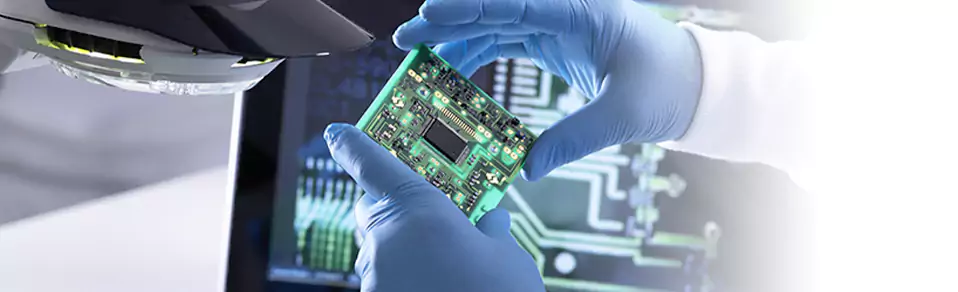
In order to help PCB and PCBA boards have the good resist to threat of dirty and various chemical corrosion, JH PCBA normally brush solder mask oil onto PCB board surface and spray conformal coating to PCBA boards to protect bare boards and exposed components joints, so that we can use boards even in dusty environments and prevent oxidation and chemical corrosion.
2)Long Product Life Cycle
the design life of automotive is generally around 15 years or 200,000 kilometers the supply cycle may be as long as 30 years.
3)High Reliability
The PCB and components mounted on the boards must follow high-reliability standards because it is related to the safety of operation and life. Generally
4)High-Security Requests
In addition to providing comfort, the automotive must ensure the safety of the entire vehicle system and even zero defects. In addition, with the popularization of electric vehicles, the importance of information security is becoming more and more prominent. As a real-time online device, The communication between it and the network, including the communication with the in-vehicle network, requires data encryption.
5)From the first process to the end, automotive PCBs whole manufacturing process must be traceable
Automotive PCBs have strict quality requirements, and whole process must be traceable. From the first process to the end, the entire manufacturing process of every automotive PCB board is recorded in a "PPAP level 3 required" report, including material used, manufacturing process flow, operators, machine specifications, quality control details, test reports etc. The "PPAP level 3 required" report and a COC report are delivered with the automotive PCBs to the buyer. Meanwhile, JH PCBA's intelligent management system records all information for traceability.
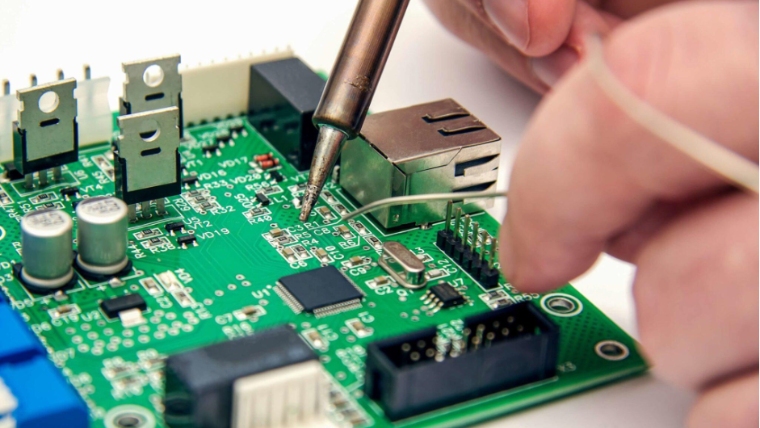
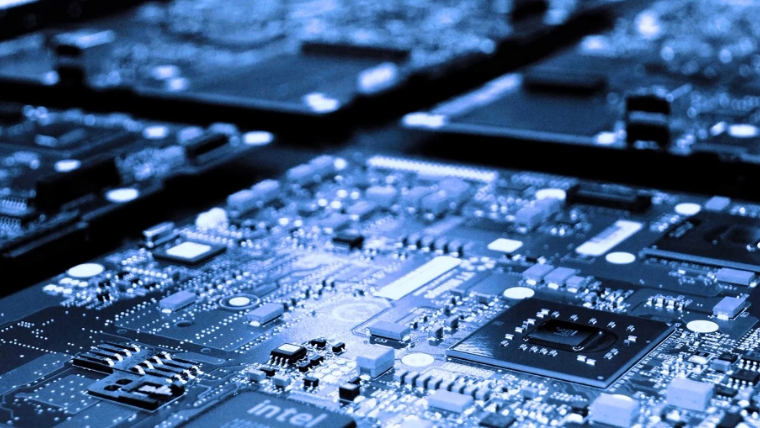
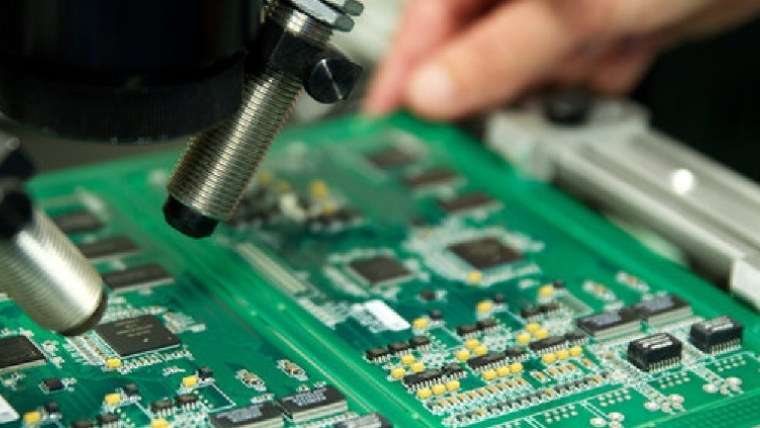
JH PCBA's Capabilities of Automotive Electronics
JH PCBA specializes in automotive electronics, offering advanced PCB manufacturing capabilities tailored for the automotive industry.
With expertise in producing high-quality, multi-layer rigid and flex PCBs, JH PCBA supports complex automotive systems, including ADAS, power management, and infotainment solutions.
The company ensures reliability and performance, meeting the stringent standards required for automotive applications.
Production line | ||
---|---|---|
![]() |
![]() |
![]() |
![]() |
![]() |
![]() |
Assembiy Type | Production Equipment | Inspection and Testing Equipment |
---|---|---|
Surface Mount (SMT) | SMT Production Lines:4 | AOI:2 |
Through Hole(THT)/Hand Soldering | THT Production Lines:2 | X-RAY BGA Inspection Machine:1 |
Mixed Technology(SMT+THT) | YAMAHA High-speed SMT Machine:6 | SINIC-TEK SPI:1 |
Finished Product Assembly | GKG Solder Paste Printing Machine :4 | Smart SMT First Article Inspection Machine:1 |
Type of Test
|
Jintuo Refiow Soldering Machine:2 | Electree icroecone with meaeurement functient 2 |
Nitto Wave Soldering Machine:1 | Other Equipment
|
|
Hand Soldering Lines;2 | ||
FunctionalTest Lines:2 | ||
Conformal Coating Spraying Machine:1 |
Quality Control | ||
---|---|---|
![]() |
![]() |
![]() |
![]() |
![]() |
![]() |
Testing Equipment | ||
---|---|---|
![]() |
![]() |
![]() |
![]() |
![]() |
![]() |
Full process capability:
– BGA and Micro BGA placement – Cable and Harness Assemblies – Box assembled – IC programming – ICT/FCT – X-ray inspection – AOI
Automotive specific process
– Class 100 Clean Room – Selective Solder Wave – High Voltage Test – Aging test – Conformal Coating – Aqueous Washing – Third-Party Reliability Testing
Automotive PcB -The Completed FAQ Guide
What ls Automotive PCB?
Vehicles use printed circuit boards (PCBs). lt is a small printed circuit board with electronic controldevices on it. These components can be programmed to carry out specifc commands. A PCB is responsible for almost everything in a car. This circuit board is simple to repair. AutomotivePCBs are highly reliable and safe to use because they are designed by professional engineers. They are, however, not cheap to buy.
Why We Use Automotive PCB?
The use of Automotive PCB is becoming increasingly widespread, largely because of the growingdemand for electrical power in vehicles. This electrical power is used to power everything from theengine to accessory car electronics. While most vehicles run on gasoline, many electric vehicles nowuse electricity for power. As the future of transportation shifts towards electrifed cars, automotive PCBs will becomeincreasingly important for these vehicles. Not only will these boards increase the effciency of carsbut they will also make repair and replacement easier.
How Many Types of Automotive PCBs Are There?
Automotive PCBs are classifed into several types. They are built to withstand a wide range ofenvironmental conditions. Because of their weight, these PCBs are typically made of copper, andthey must withstand both internal and external heat. As a result, there are special requirements folautomotive PCB heat resistance. Some of the most common types of automotive PCBs are listedbelow. You may be wondering how to tell the difference between the various types of PCBs
How to Choose the Proper Material for Automotive PCBs?
Automotive PCBs must pass stringent reliability tests, including high temperature and humidity.Defects, such as Conductive Anodic Filament (CAF), which can cause short circuits betweenconductive traces and Copper Clad Laminate, must also be avoided. The table below describes thevarious types of PCB substrates used in automobiles. By following these guidelines, you can selectthe best one for your needs.
PCBA Application Field

Medic Equipment
PCBA in medical equipment ensures precise and reliable functionality for devices such as diagnostic machines, imaging systems, and patient monitors.

Telecommunication
In telecommunications, PCBA is critical for the operation of networking hardware, base stations, and communication devices.

Consumer Electronic
PCBA in consumer electronics includes components for smartphones, tablets, smart TVs, and wearable devices.

Industrial Control
For industrial control applications, PCBA is used in machinery control systems, automation equipment, and monitoring devices.

Hi-Tech Agricultural
In hi-tech agriculture, PCBA is employed in smart farming solutions such as sensors, automated irrigation systems, and agricultural drones.

New Energy Automobile
PCBA in new energy vehicles, including electric and hybrid cars, supports critical functions such as battery management systems, motor control, and energy management.